Have you ever wondered how intricate designs are cut into glass and metal? Surely no human can have that amount of skill and precision–that’s why CNC Machines do it!
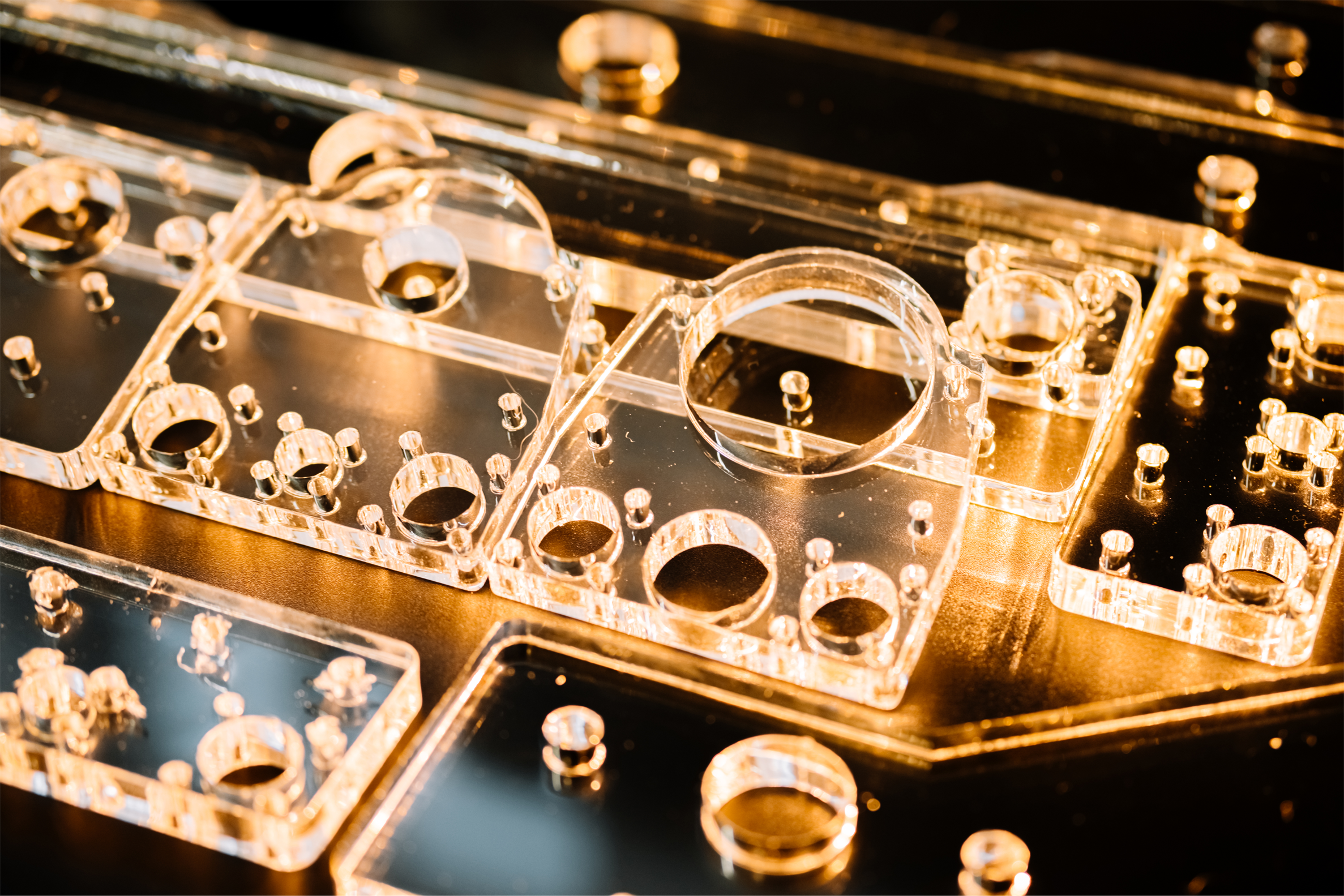
CNC 101
A CNC Machine is a specialized piece of equipment that allows those in the glass industry to cut glass. With a CNC machine you can get a really precise cut that would otherwise be impossible to obtain with regular scoring and breaking by hand. It also allows us to do special shapes with high precision.
A CNC machine is also used to automate the glass cutting process. This is why some companies have high minimum quantities to order custom sizes! This is because when you decide you want to use the CNC to cut something, you have to feed it an entire sheet of glass.
You wouldn’t load up an entire sheet to cut one piece unless you need that super high tolerance, which is why 1 piece can cost as much as 30 pieces of the same size because once you cut into a stock sheet, the remaining pieces are considered cutoffs and may never be used for new orders that come in.
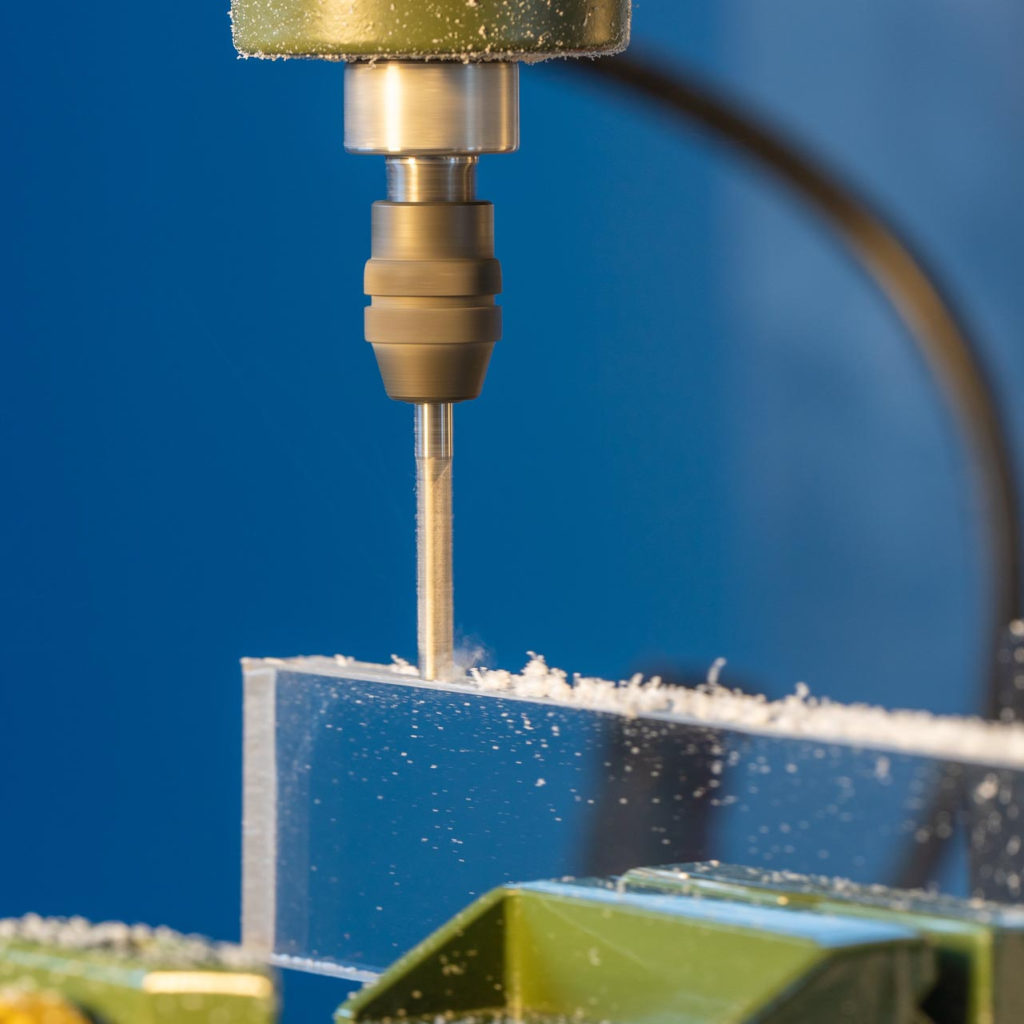
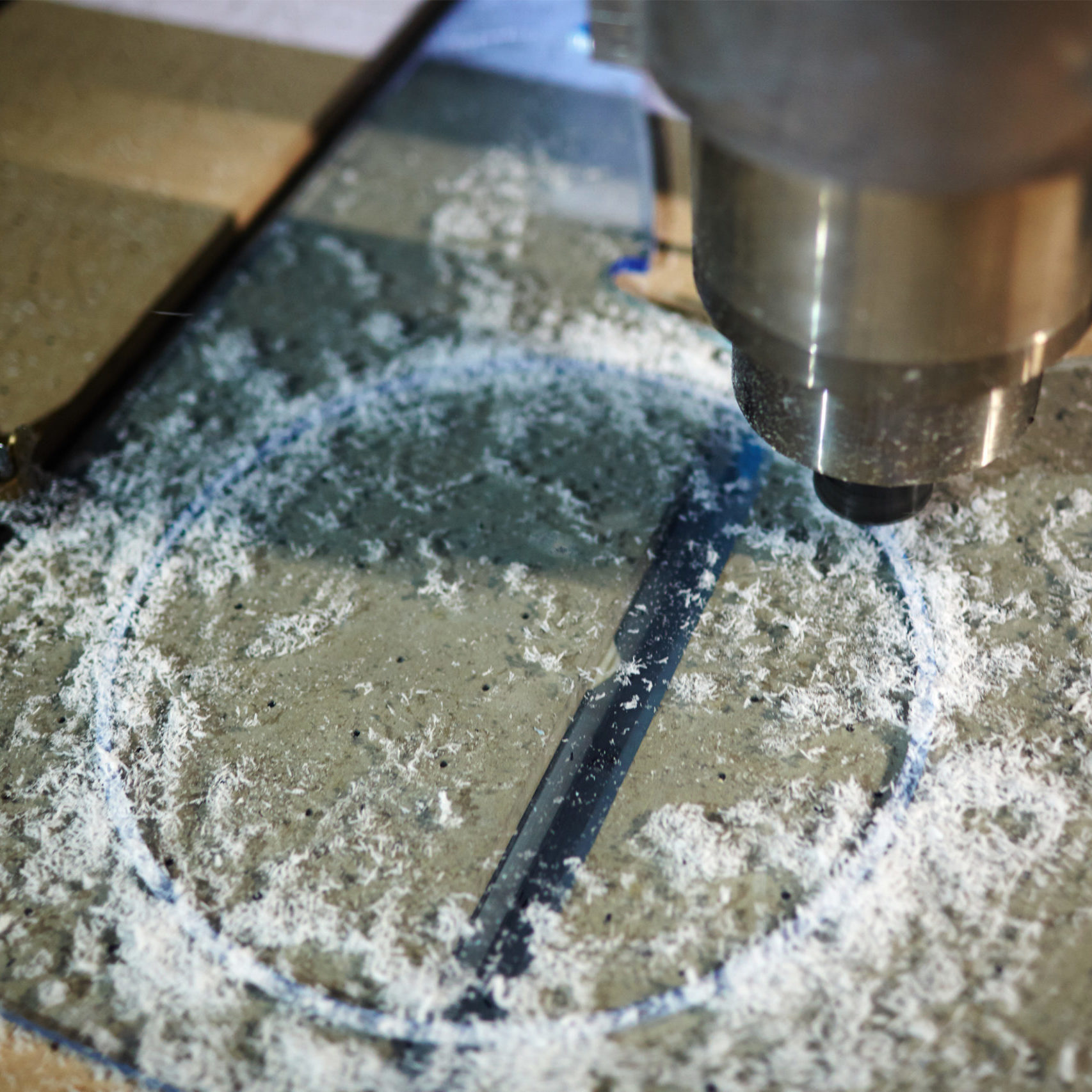
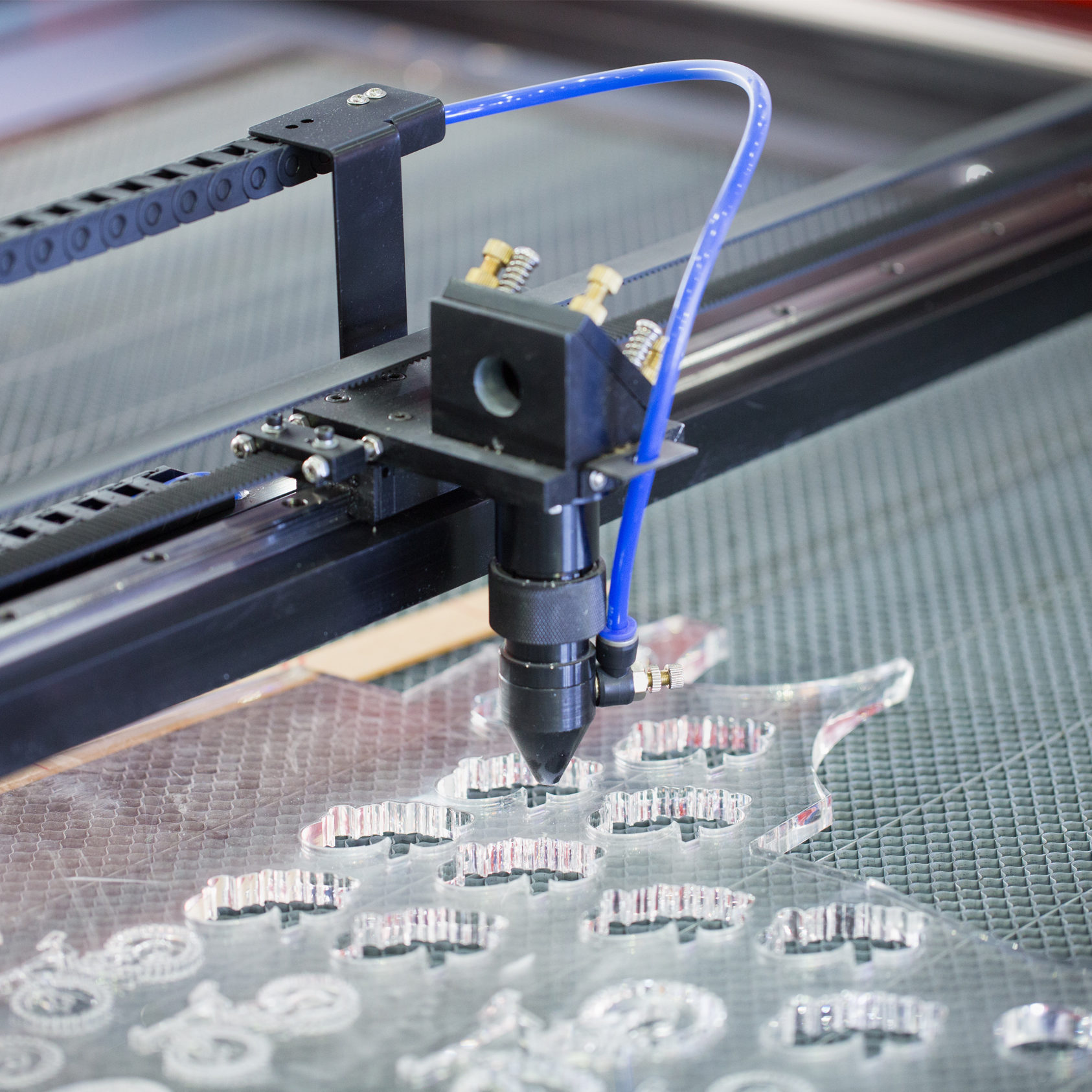
How It Works:
DXF Files
It all starts with a DXF file. This is just a fancy term for a diagram of a part that needs to be cut to a certain size and shape within a specific tolerance. It has to be in DXF file format because that is the type of file the CNC machine can take in to perform the action on the glass stock sheet.
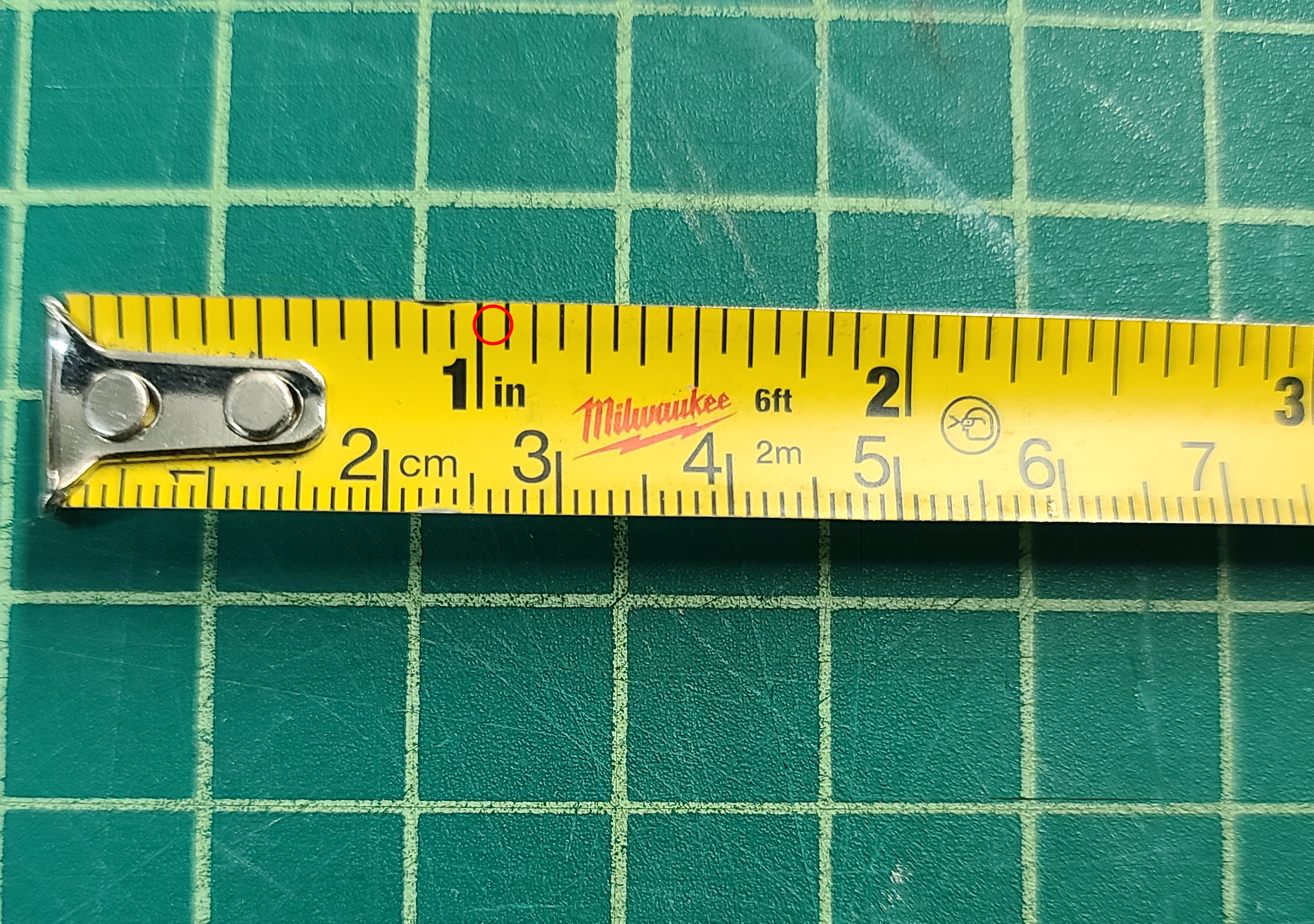
Most people don’t realize this but when you order a piece of custom size glass, there is a cutting tolerance. It is different from company to company and for our cuts our tolerance is +/- 1/16”.
When the tolerance needs to be tighter it is definitely doable and depending on how tight, the CNC is the go to method for achieving it.
For example, if you need something cut to +/- 0.001mm, that is basically impossible to do by hand. The equipment used to cut the glass itself has a lower standard of measurement, which could mean hours of sanding if the cut is too large. This would not be time or cost effective.
The DXF file carries a ton of information that allows you to also optimize the material you are cutting into.
For example: If you have to create 100 pieces that are 2×3 inches, to get the most out of the material you’d need to figure out how each cut will be made.
This will optimize the amount of pieces one stock sheet that has a fixed size of 32×50 inches can make. By optimizing how it is cut you can use less material and have less waste.
You can open a DXF File with a CAD program or in Adobe Illustrator.
Importing & Calibration
Once you have your diagram ready to go, you import that into the machine and calibrate the machine to the material you have.
If you are using 1/4″ float glass on a CNC machine, you have to dial the CNC in to be more gentle. Metal will take a higher setting. If the CNC is too vigorous, it can seriously damage the edge of the glass to the point of it being unusable.
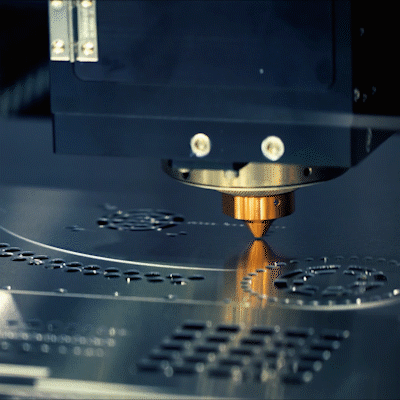
Depending on the part being made, that could be a deal breaker on the edge finish. If you need a flawless mirror coated edge that fits into a robotic machine, you need to utilize every millimeter of surface area. If it is not calibrated correctly it could also straight up shatter the glass.
Once you feed in the instructions to the machine and calibrate it you simply load up the glass and let the machine do its work. With different machines it will execute the instructions differently.
Waterjet CNC
A waterjet CNC works great if you know how to dial the settings to work with glass. A waterjet takes the instructions and comes in from the edge of the glass and routes out the glass using abrasive water.
It’s really cool because you can still get a sharp edge even though it is a circular knob on the end. The only thing it can’t do is sharp holes within the glass because of the shape of the rod.
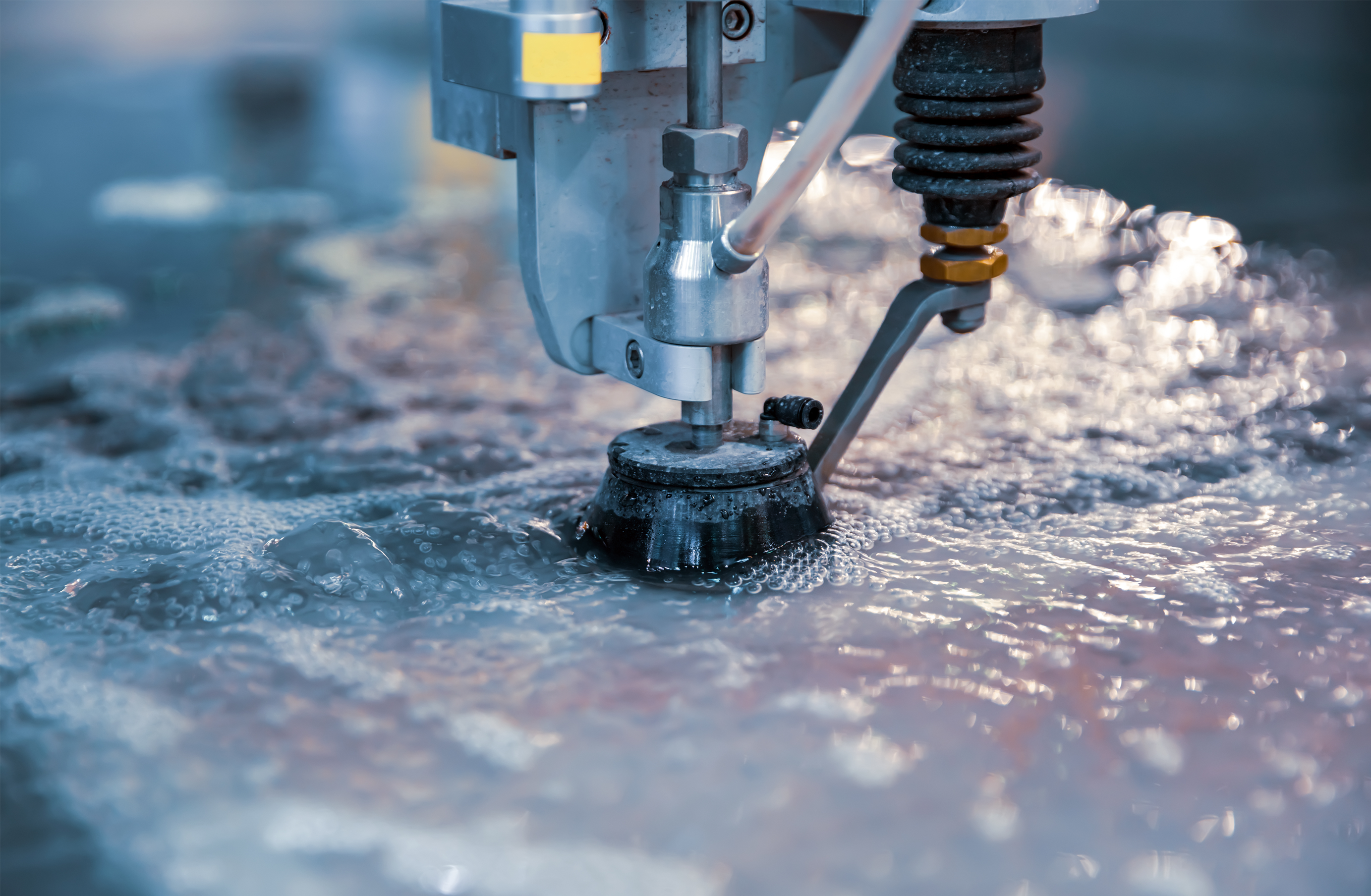
That means it really is great for any glass cuts like rectangles, trapezoids, triangles, pentagons, and weird shapes. Basically anything that does not have a square or sharp hole on the inside.
Circular holes can be possible but may impact the flatness of the glass once it has been cut like that.
Garnet
Garnet is the material used that is mixed with the water to allow the water to cut the material. The more garnet you use, the faster it will cut through the material.
- The garnet is put into the hopper
- The garnet looks like brown sand
The hopper has a warning light that lets you know when it is getting low. When the light comes on you have about 1 hour left before you need to seriously refill.
When the computer control is asking for garnet, it gets funneled through a hose. Then it makes it way through the machine, getting pushed up by air pressure and vacuumed into the gantry. It then goes into a mixing chamber.
Next, it goes through a metering disc which looks like a metal circle with a hole in the center. This controls how much garnet comes through.
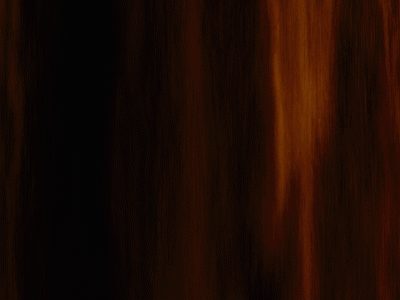
The garnet could be reused but it is not really recommended. Once it is used, it gets mixed in with any trace elements of what you were cutting. You want it to be nice and clean for the best result.
It also changes form a bit when it is first used to cut something– it explodes! It may not have as much mass the second time around that could be necessary to cut certain materials.
Once the tank starts to get full of garnet and other things, a septic tank company usually comes by to remove what’s in the tank once or twice per year.
Cutting Head
The cutting head has a diamond orifice that allows the pressure to build to make it stronger. Kind of like what happens when you put your thumb over a hose at home! The end goal is to increase the distance and pressure as the water comes out.
There is a hose attached to the cutting head that feeds the garnet into the water mixture. You can find it just below the diamond orifice. Then the mixture goes through the focusing tube and cuts the material.
While you do not necessarily need to use garnet to cut things, there is a rule of thumb. If you can cut the material with scissors, you can use straight up water to cut it with the waterjet. Since glass cannot be cut like that, it does require garnet to cut. This process produces a sanded edge that makes it safe to handle.
Scoring Wheel
There are other types of CNC machines that are designed specifically for glass cutting. Instead of having a regular head on it that would be used on a waterjet, it has a scoring wheel.
This allows the CNC to score the glass directly which allows for more flexibility in the cut, specifically when cutting out holes within the glass. In this case the CNC simply scores the glass and then you have to break it afterward by hand.